Expert injection moulding product design & development
Whether you're an entrepreneur with a breakthrough idea or a business needing a scaled supplier, our end-to-end design and development service provides the expertise, technology and support to bring your vision to life. With over 30 years of manufacturing experience and ISO 9001 certification, we're your trusted partner in product development.












Preliminary costing and consultation: Product conceptualisation
- Initial consultation to understand your product requirements
- Assessment of injection moulding feasibility
- Production volume planning and timeline development
- Material selection guidance and recommendations
- Preliminary cost considerations

Product design & development: Specification and 3D models
- Custom product design and optimisation
- CAD modelling and technical drawings
- Design for manufacture (DFM) analysis
- Detailed quotation for tooling and production
- 3D printed prototypes for concept validation

Tooling: Engineering Your Success
- CAD tool design and consult
- Precision tooling
- Quality control checks throughout machining
- Initial testing and adjustments
- Tool validation and documentation

Product trial & approval :
Perfecting your product
- Initial trial runs and testing
- Quality assurance checks
- Product refinement if needed
- Customer approval

Full production & supply:
Delivering quality at scale
- 24/5 Production availability of product
- Quality management
- Custom packaging solutions
- Inventory management
- Flexible services
- Tool servicing

Discover the advantages of plastic injection moulding for your business
Optimise your design with injection moulding—a highly adaptable, cost-efficient solution for delivering precision-engineered parts at scale. Whether you are developing a new product or refining existing ones, our comprehensive suite of injection molding capabilities provides significant technical advantages for your products.
Cost-effective at
scale
As production volumes increase, the cost per unit dramatically decreases. Once your mould is created, each part can be produced rapidly and consistently, making injection moulding particularly economical for medium to high-volume production runs.
Design freedom & complexity
Create complex geometries and intricate features that would be impossible or prohibitively expensive with other manufacturing methods. From snap-fits to living hinges, injection moulding enables sophisticated design features while maintaining structural integrity.
Consistent quality & precision
Every part is produced with exceptional accuracy and repeatability. Our advanced injection moulding systems maintain tight tolerances and consistent material properties across production runs, ensuring your products meet the highest quality standards.
Versatile material selection
Choose from engineering-grade plastics with specialised properties like flame retardance, impact resistance, and UV stability. We also offer biodegradable options, high optical clarity, and custom finishes - ensuring the perfect material for your application.
Understanding plastic injection moulding
Discover the process of plastic injection moulding.
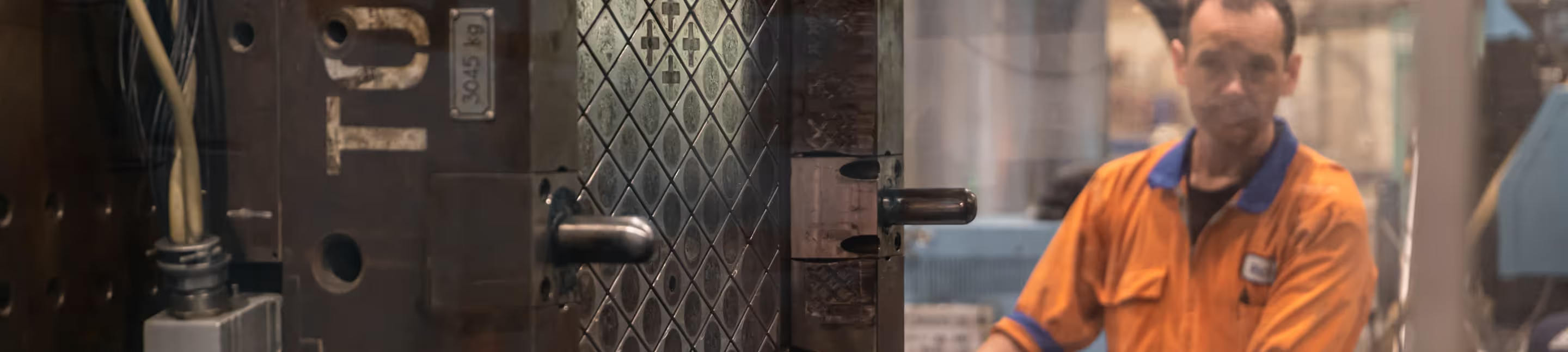
Designing for a sustainable future

Material selection
Choose from our range of eco-friendly materials, including recycled polymers, biodegradable options, and materials designed for recyclability. We'll help you select materials that balance environmental impact with performance requirements.
Design for longevity
Create products that stand the test of time through robust design principles, appropriate material selection, and quality manufacturing. We'll help you identify potential wear points and design solutions that extend product life.
Circular design principles
Create and design circular manufacturing systems that allow products to feed into new stock.
Waste reduction
Optimise your design to be easily recyclable to New Zealand and international standards. Design focus on end of life as well as functionality.
Industry-leading recognition backing our promise to quality and sustainability

Computer model design
We'll bring your product to life in the digital world first, creating detailed 3D models that let you see exactly how your product will look and function. Our design team works closely with you to perfect every detail, making sure your product isn't just beautifully designed, but also ready for efficient manufacturing. Before any tooling begins, we'll test how all the pieces fit together and identify any potential manufacturing challenges – saving you time and money.

Technical Documentation
Getting the documentation right is crucial for successful manufacturing. We'll create a complete set of technical drawings and specifications that cover everything needed to make your product perfectly, every time. From precise measurements to assembly guides, material choices to quality standards – we document every detail so there's no room for error. Think of it as your product's blueprint for success.
3D printed or CNC prototypes: Experience your product before production
See and feel your product before moving to full production. Our rapid prototyping service lets you validate your design, test fits and functions, and make refinements early in the development process. We can produce precise 3D printed parts for smaller components and create large-scale CNC'd prototypes for more substantial items or complete assemblies. It's a quick and cost-effective way to ensure your product is exactly right.
Validate your design with tangible prototypes.
Test fits and functions before production.
Refine your product quickly and cost-effectively.

Precision tool making
Expert tool design and manufacturing for perfect parts, every time
Design for Performance
Advanced cooling systems and optimised material flow for faster cycle times and better part quality
Built to Last
Premium tool steels and precision engineering ensure longevity and consistent production quality
Smart Solutions
Innovative features like replaceable inserts and modular designs for cost-effective maintenance and modifications
ISO 9001: Quality Assured
Decades of experience combined with ISO 9001 standards, rigorous testing and validation.


Add branding, information and graphics to your products
Enhance your products with high-quality custom printing. From crisp logos and serial numbers to safety information and usage instructions, we can add permanent, professional printing directly to your injection moulded parts. Our printing solutions ensure your branding and required information remain clear and durable throughout your product's lifetime.
Permanent, fade-resistant printing
Precise alignment and placement
Range of colours available
FAQs
Get answers to common questions about injection moulding product design and development.
Process timelines can vary based on project complexity. Typically, initial designs take 2-4 weeks. Final production timelines depend on the volume and material selection.
Cost considerations include material type, production volume, and design intricacies. We provide detailed quotes after assessing your project requirements. Budgeting for prototyping is also essential.
At Uniplas, we are committed to safeguarding intellectual property. We are happy to sign and work within the terms of clients' NDAs, ensuring sensitive information remains secure. Clients also retain full transparency and control over their tools, with exclusive ownership guaranteed.
We work with a wide network of trusted suppliers, giving us access to an extensive range of materials. Additionally, we can order custom blends to ensure the exact physical properties needed for your project are met. If your requirements include environmentally friendly options, we can source materials specifically designed to align with your sustainability goals.
We cater to a wide range of production needs, from small to large-scale manufacturing. Typically, volumes required to qualify for injection moulding range from 100 to 1,000 parts. Our flexible processes ensure efficiency, quality, and cost-effectiveness, regardless of order size
Featured projects and stories
Why choose Uniplas?
Made in
New Zealand
Local manufacturing ensuring quality control, Shorter lead times, and manufacturing transparency.
Sustainable manufacturing
Committed to environmental responsibility with one of NZ's largest rooftop solar installations and sustainable practices.
ISO 9001
certified
Internationally recognised quality management system ensuring consistent, high-quality output.
Engineering
expertise
Decades of injection moulding experience combined with advanced manufacturing capabilities.
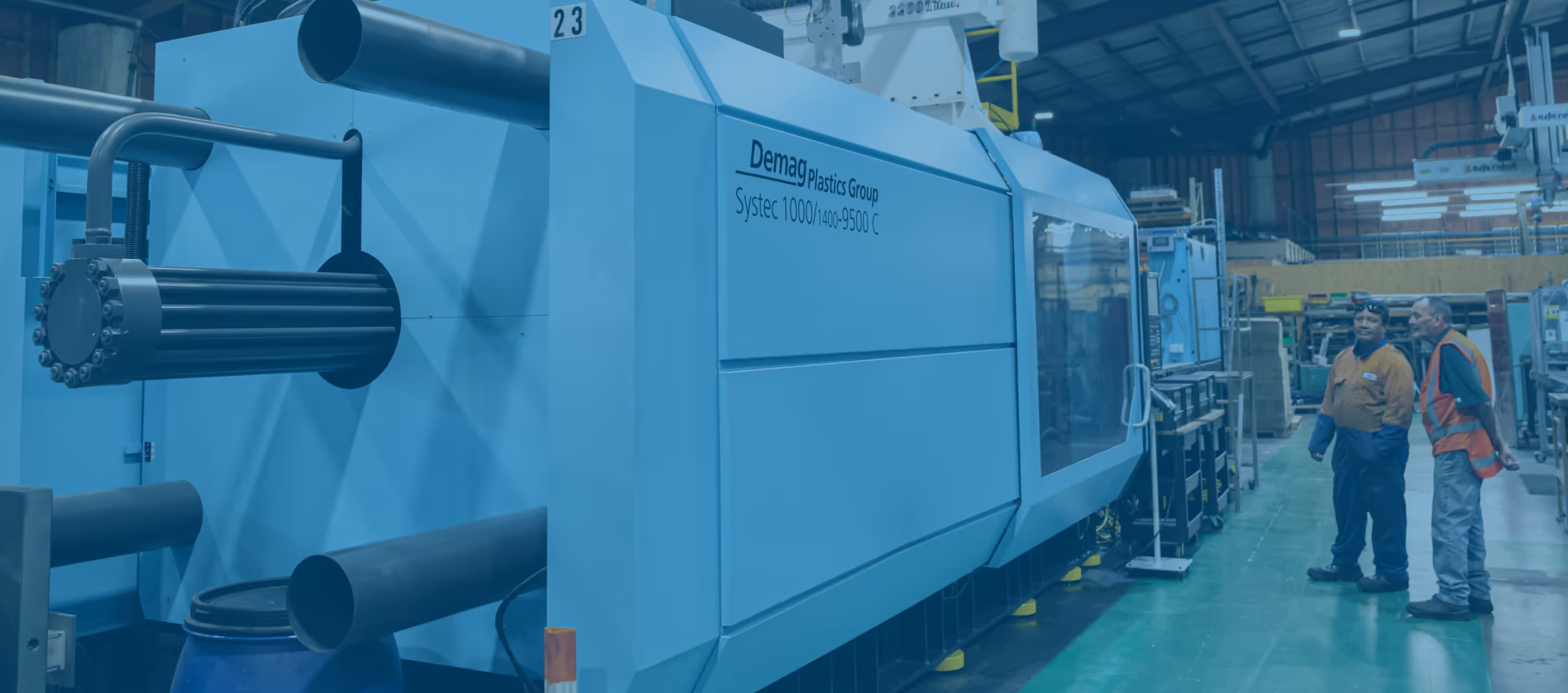
Send us a message
We typically respond within 24 hours.
Our Business hours are : Mon-Fri, 9am-5pm
Taita, Lower Hutt
New Zealand