Discover Uniplas precision plastic injection moulding
Our state-of-the-art facility combines advanced technology with decades of manufacturing expertise to produce precise, high-quality components. From concept to production, we provide end-to-end plastic injection moulding solutions tailored to your specific needs.
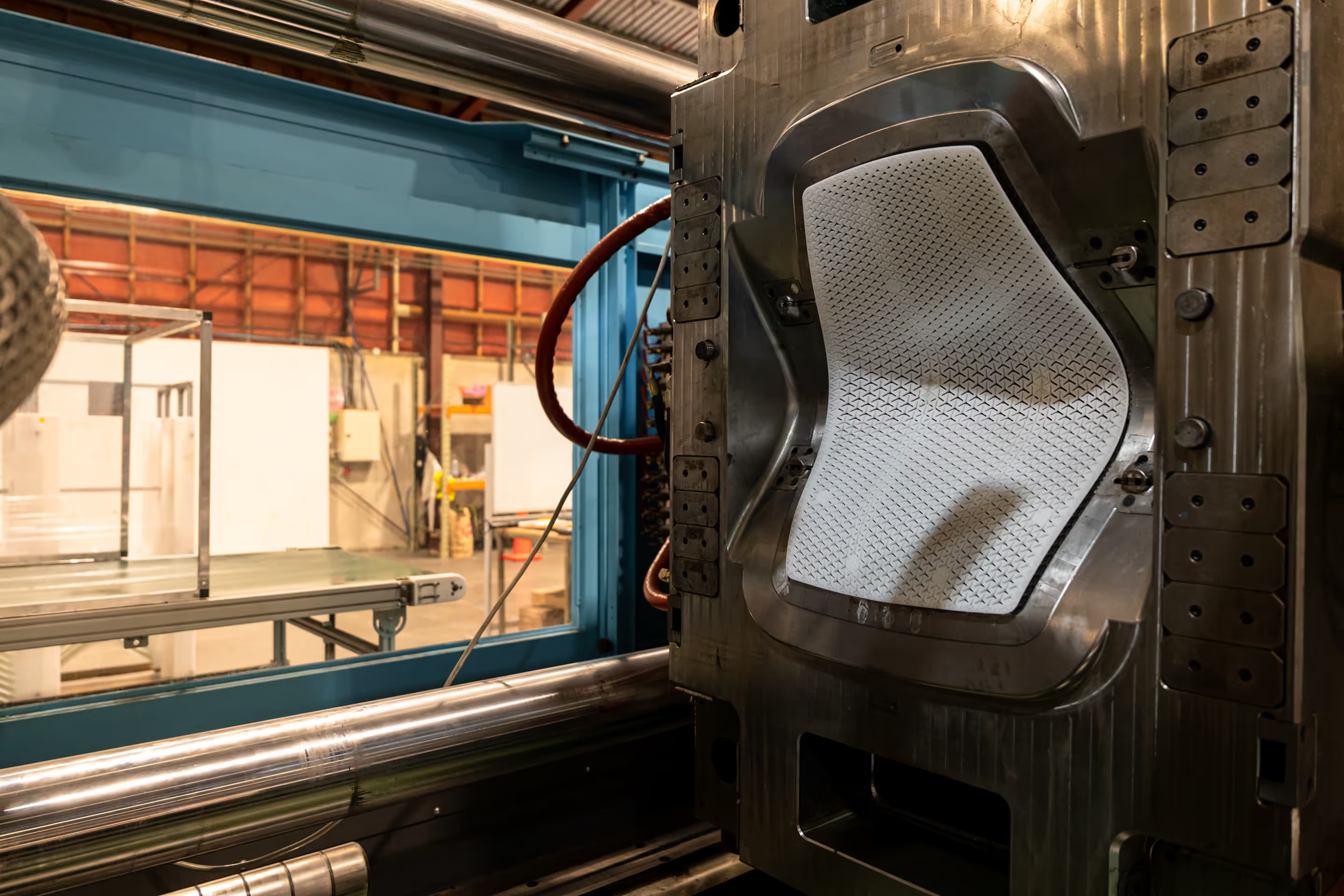
Charge the barrel
The process begins by dosing raw plastic material (usually in the form of pellets) into the barrel of the injection molding machine.
The screw inside the barrel rotates, moving the material forward while simultaneously heating and melting it. This process ensures the plastic becomes a homogeneous shot, ready for injection.
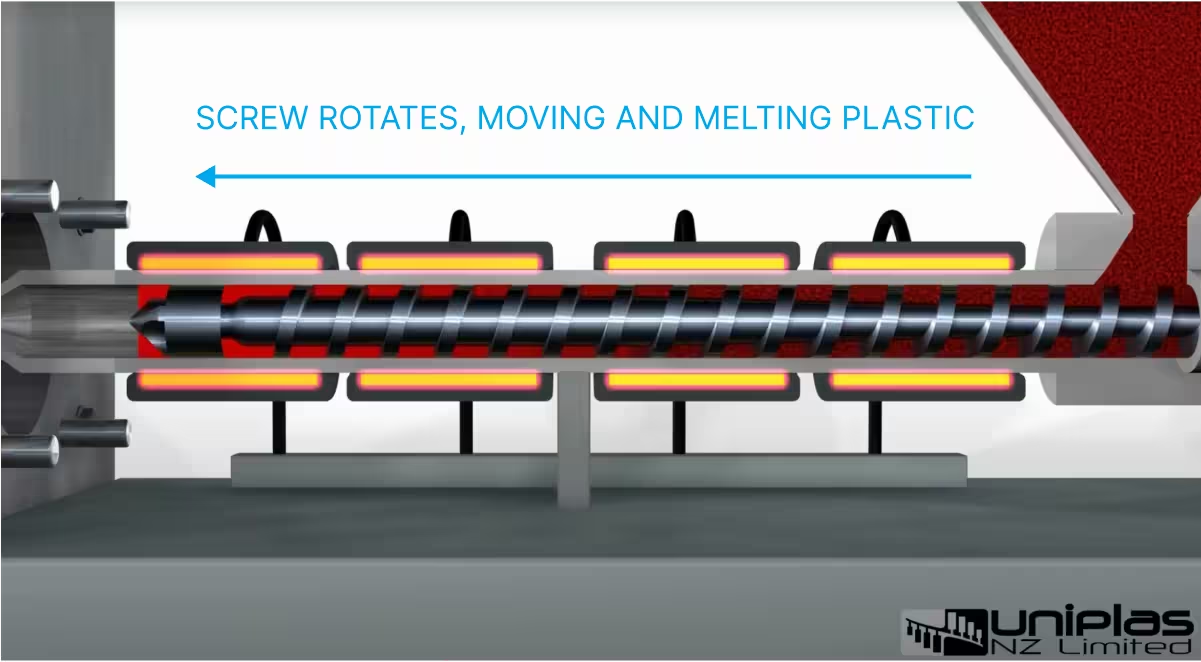
Injection
Once the material is melted and properly mixed, the machine injects it into the mould cavity under high pressure.
The speed and pressure of the injection process are carefully controlled to ensure complete mould filling and avoid defects like air pockets or short shots.
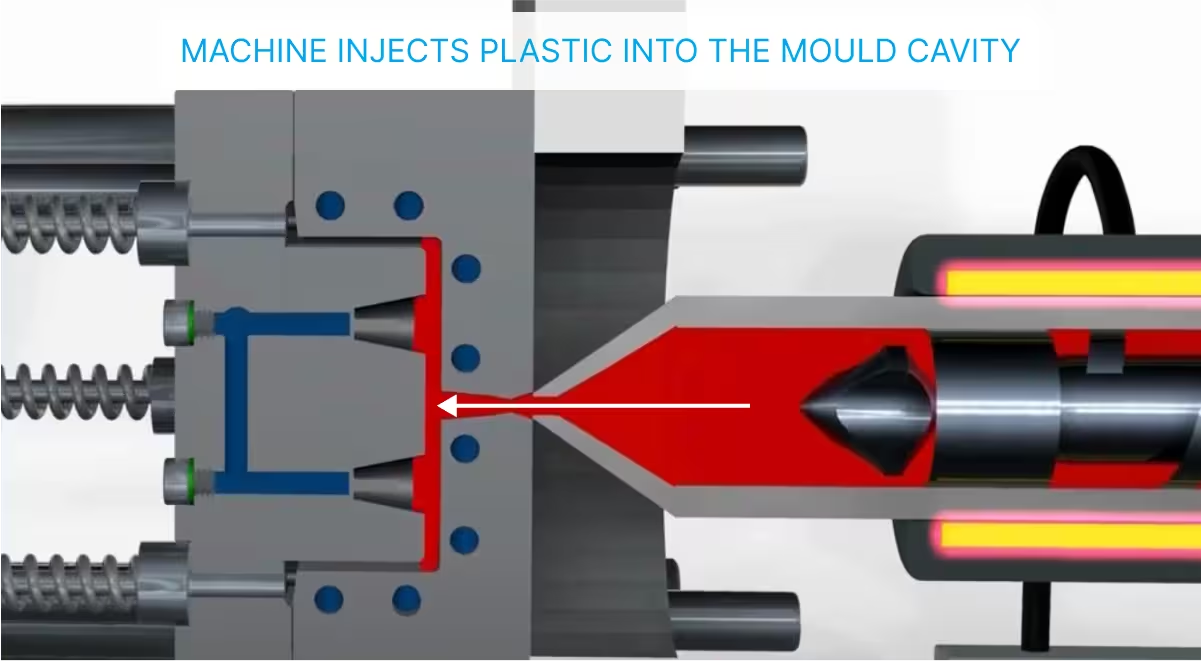
Cooling
After injection, the molten plastic begins to cool and solidify inside the mold.
Cooling time varies depending on the material, part thickness, and mold design. Efficient cooling is critical to maintaining part quality and reducing cycle times.
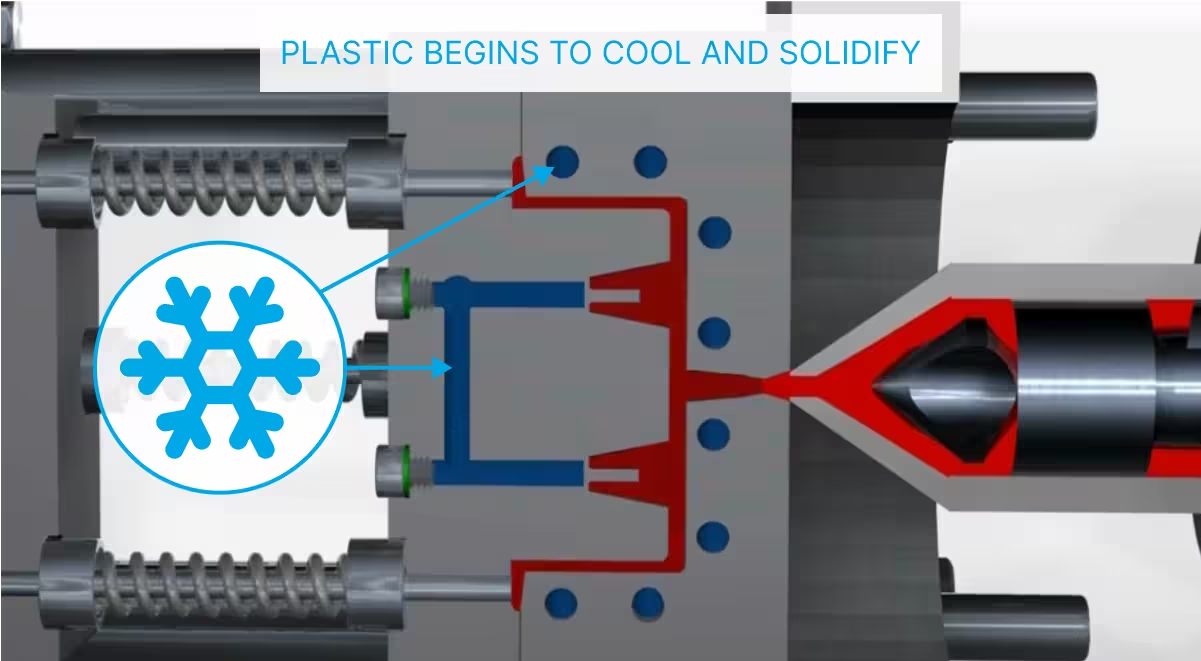
Mould opening
Once the plastic has sufficiently cooled and solidified, the mould halves separate.
The clamping unit releases, allowing the mould to open without disturbing the formed part.
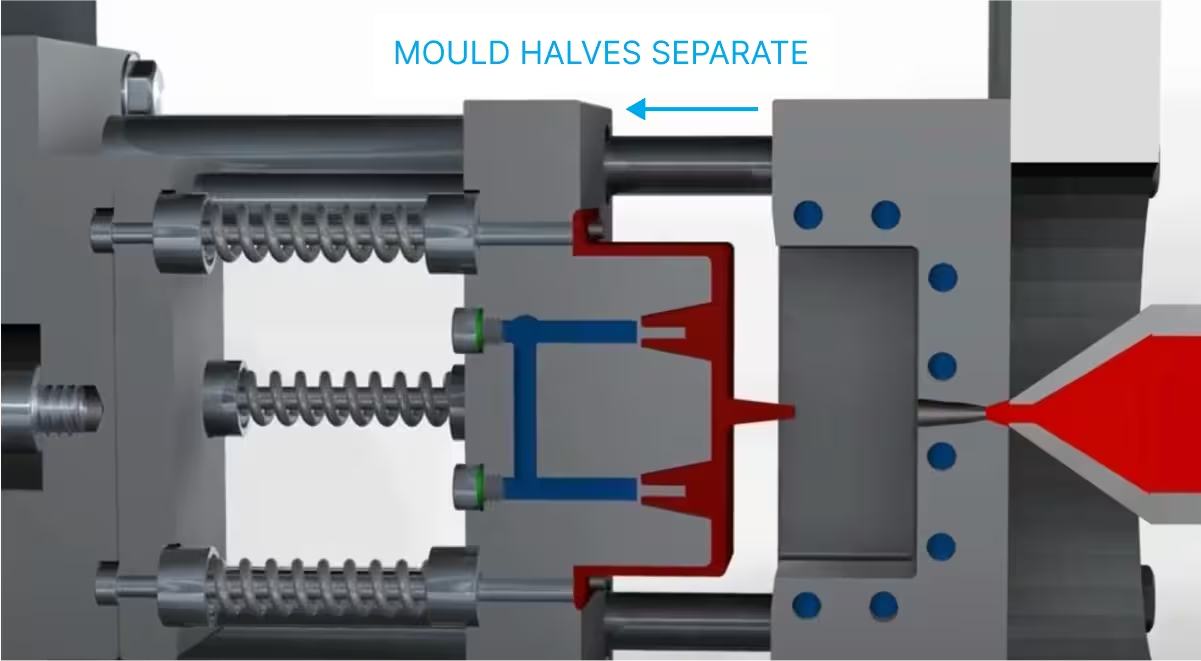
Ejection
Ejector pins or plates push the finished part out of the mould cavity. In some cases, air blasts or robotic arms assist with removal. If the part sticks, additional ejection mechanisms, such as stripper plates, may be used.
After ejection, the mold closes again, preparing for the next cycle. The clamping unit secures the mold halves together, and the process repeats.
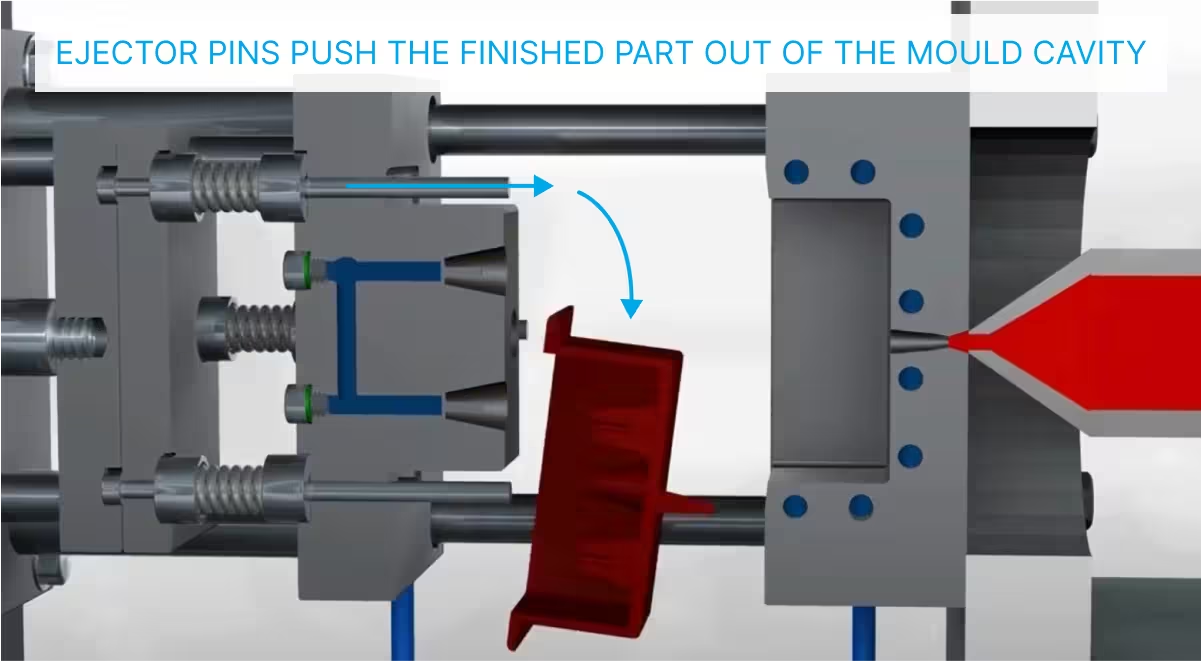
By the numbers
Delivering scale, precision and innovation across New Zealand manufacturing.
Years of combined experience
Different products manufactured annually
22t to 1100t
Machine range
Injection moulding machines
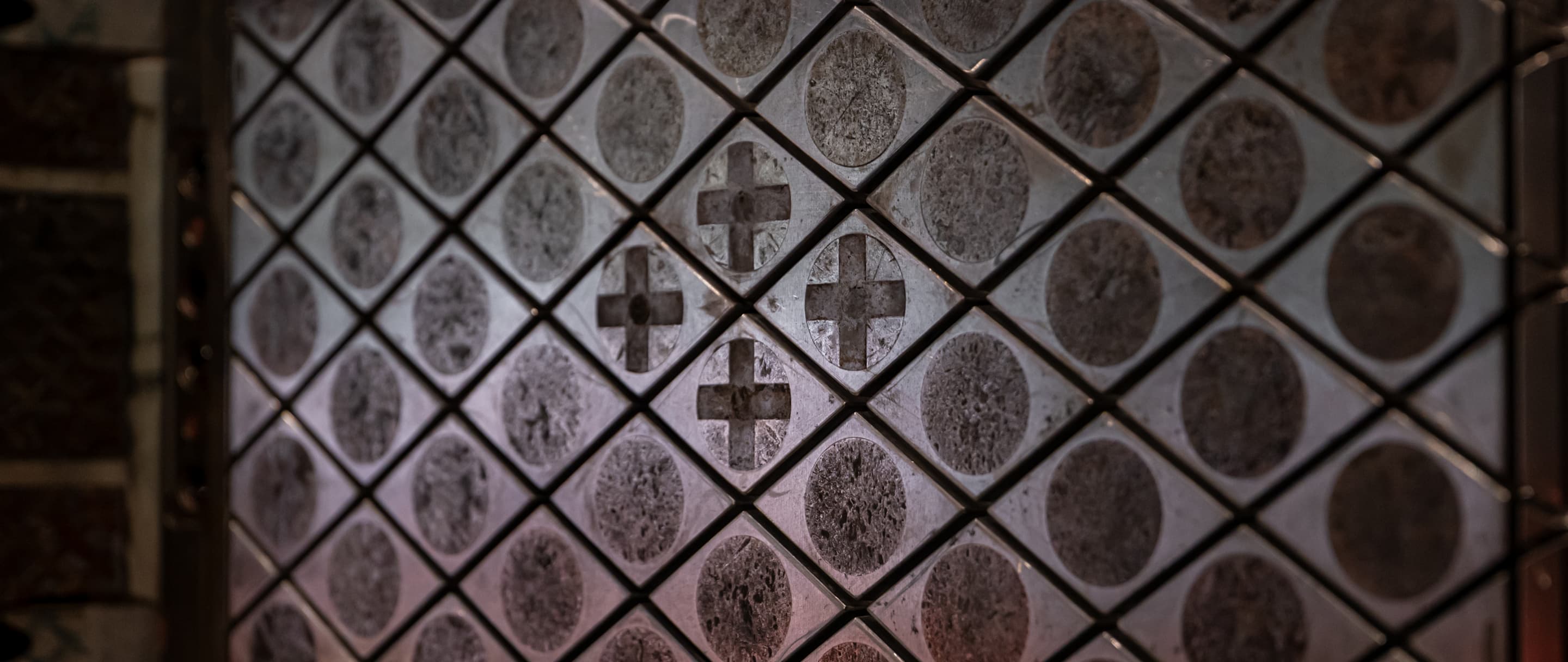
Is injection moulding the right choice?
Plastic injection moulding offers exceptional precision, consistency and scalability for plastic components. Here's how to determine if it's the ideal manufacturing method for your project.
Production volume
Injection moulding becomes increasingly cost-effective at higher volumes, where the initial tooling investment is offset by lower per-unit costs.
Design complexity
Our process excels with intricate designs, complex geometries and components with precise tolerances that would be difficult to achieve with other manufacturing methods.
Consistency & quality
Perfect for applications where part-to-part consistency, surface finish quality and dimensional stability are critical to product performance.
Material requirements
Ideal for projects requiring specific material properties such as strength, flexibility, temperature resistance, or FDA compliance across a wide range of engineering plastics.
Time considerations
While initial tooling requires upfront investment in time, once production begins, components can be manufactured rapidly and consistently.
Choosing the right plastic manufacturing process
Different plastic manufacturing methods offer distinct advantages depending on your project requirements. Understanding these options helps ensure optimal results for your specific needs. Explore the most common processes below to determine which might be best suited for your product before consulting with our team.
Injection moulding
Example: Bread Crates
Use cases: Best suited for high-volume production of detailed, complex parts. High upfront tooling costs but low per-unit costs at scale. Produces strong, consistent parts with tight tolerances.
3D Printing (Additive Manufacturing)
Example: Prototype models
Use cases: Best for low-volume, custom, or prototype parts. No expensive moulds required, but much slower and less cost-effective for large-scale production.
Uniplas 3D Printing focuses on creating small to medium-sized components, primarily for prototype product development.
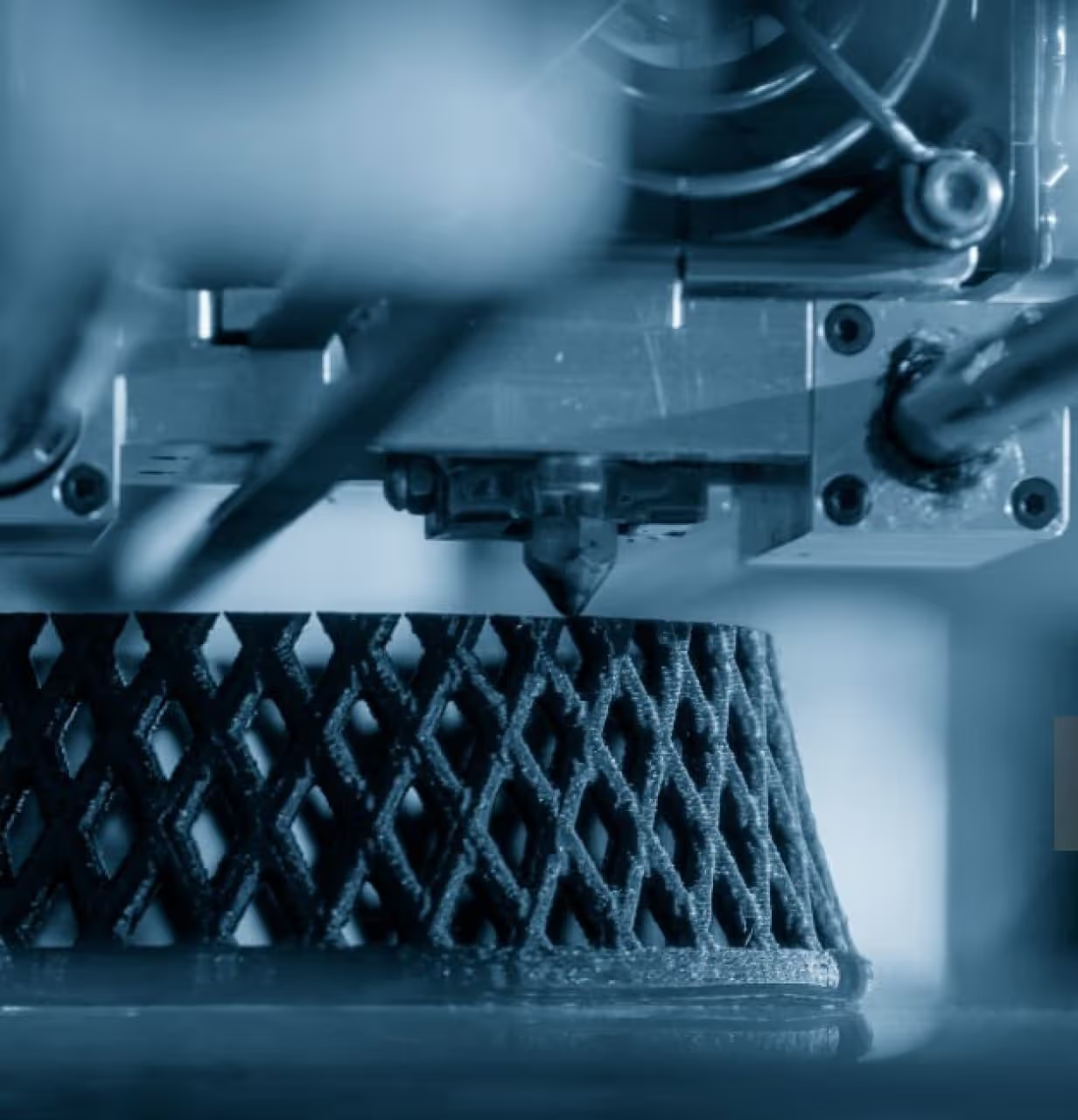
Blow moulding
Example: Plastic bottles
Use cases: More cost-effective than injection moulding for hollow objects. Best for medium-to-high volume runs. Limited to relatively simple hollow shapes like bottles and containers.
Uniplas can consult and design for these products but may outsource the manufacturing component.
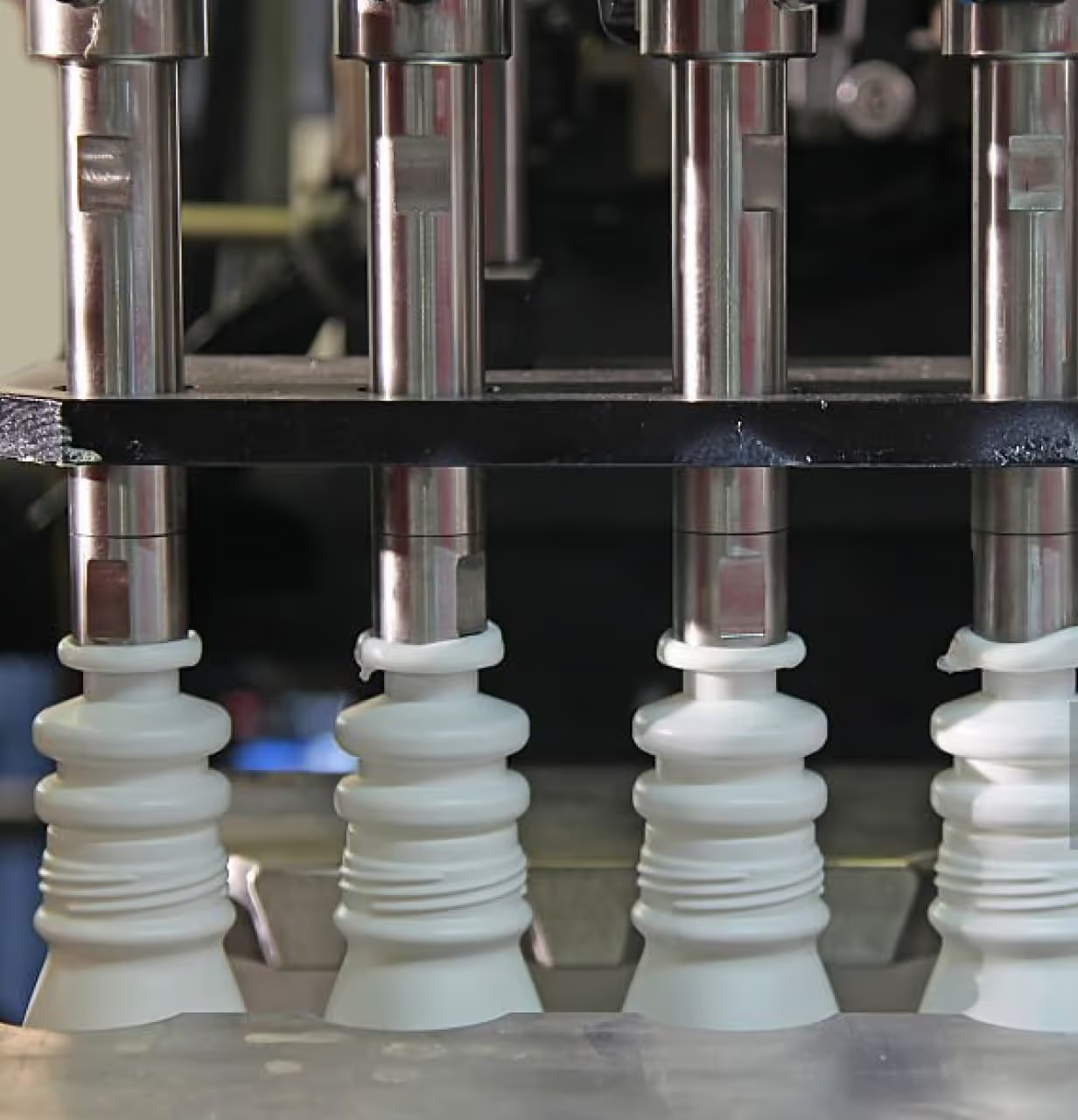
Rotational moulding (roto moulding)
Example: Large storage tanks
Use cases: Ideal for large, hollow, and durable parts. No seams or weak points. Lower tooling costs than injection and blow moulding, but higher per-unit costs, making it best for low-to-medium volume production.
Uniplas can consult and design for these products but may outsource the manufacturing component.

Thermoforming
Example: Disposable food packaging
Use cases: Faster and cheaper than injection moulding, but limited to thinner-walled products. Best for low-cost, high-volume applications like packaging and trays.
Uniplas can consult and design for these products but may outsource the manufacturing component.
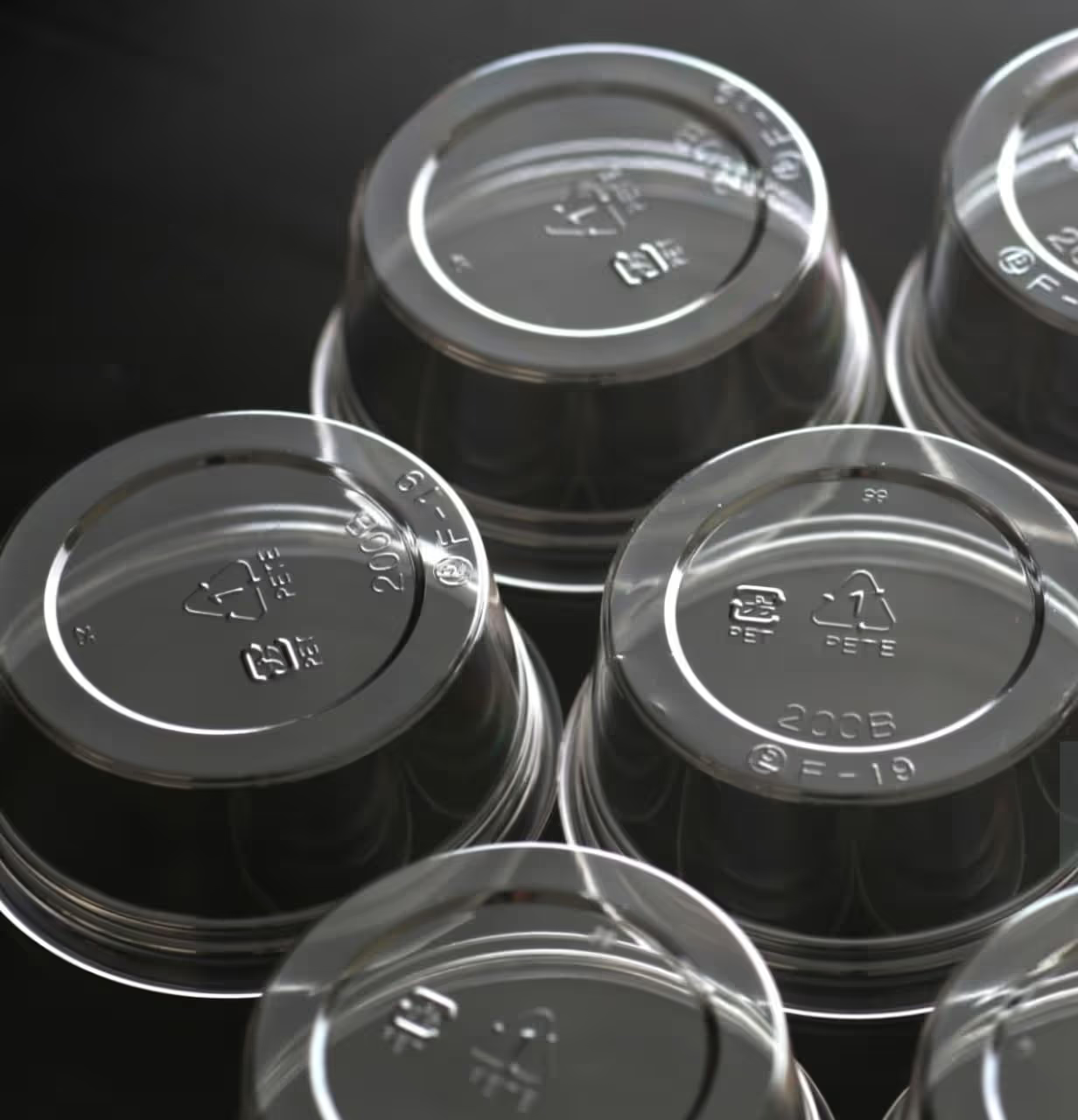
Extrusion moulding
Example: PVC pipes
Use cases: Best for continuous, uniform products like pipes, tubes, and sheets. Very cost-effective for high-volume production but limited to simple cross-sectional shapes.
Uniplas can consult and design for these products but may outsource the manufacturing component.

Compression Moulding
Example: Car tires (rubber-based plastics)
Use cases: Good for large, durable parts. Lower tooling costs than injection moulding, but slower cycle times. Best for medium-volume production.
Uniplas can consult and design for these products but may outsource the manufacturing component.
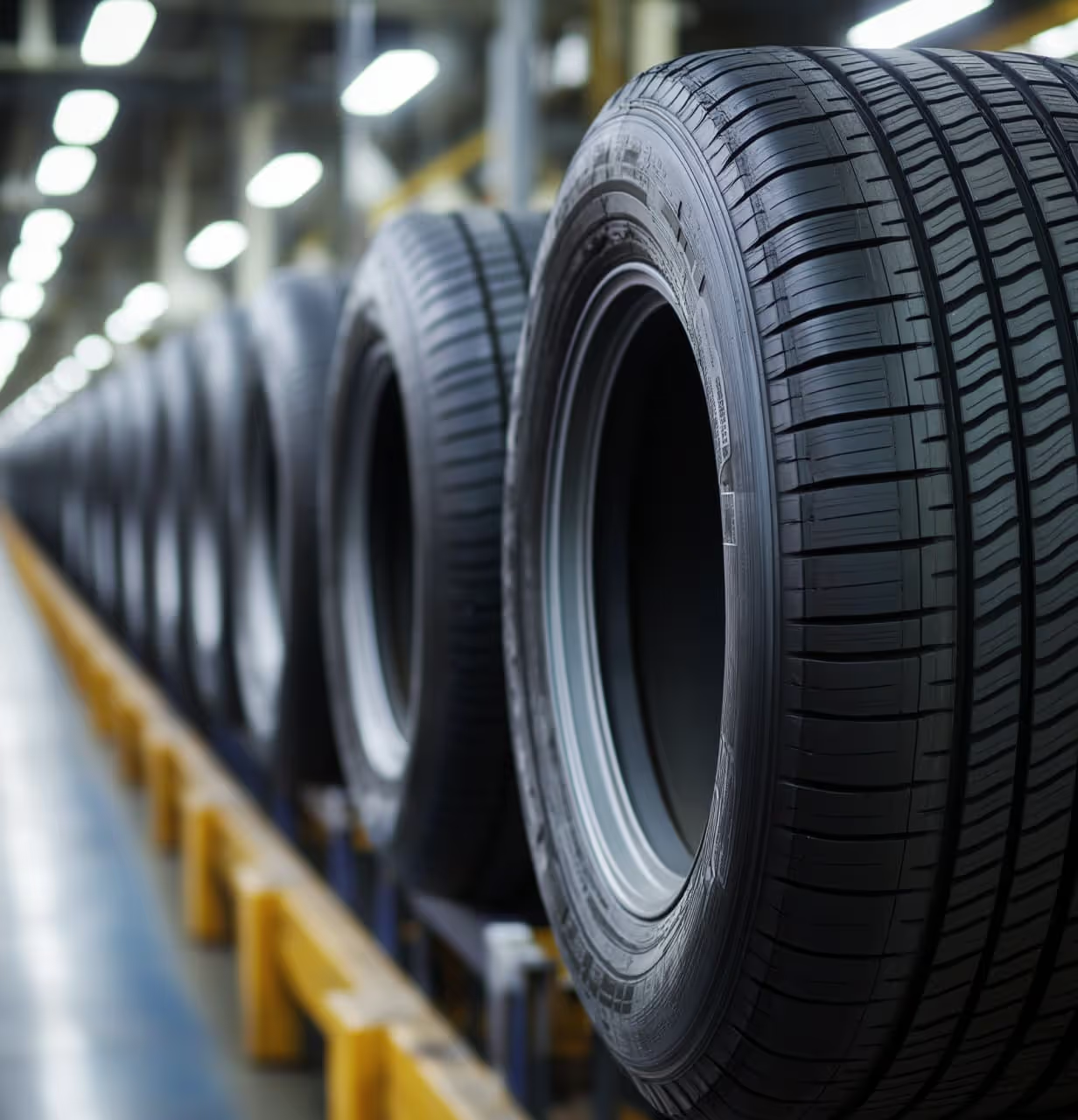
Industry-leading recognition backing our promise to quality and sustainability
Plastic injection moulding product design & development
Our expert plastic manufacturing design and development service can bring your vision to life.
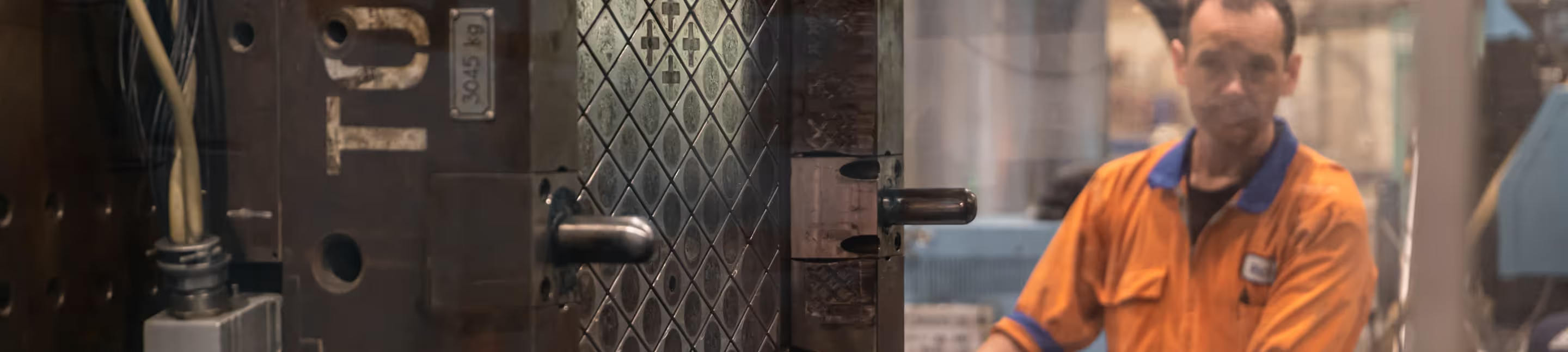
Scale production with our advanced injection moulding capabilities
Uniplas combines advanced machinery, technical expertise and rigorous quality control to deliver injection moulding solutions across diverse industries. Our comprehensive capabilities ensure we can handle projects of any complexity or scale.
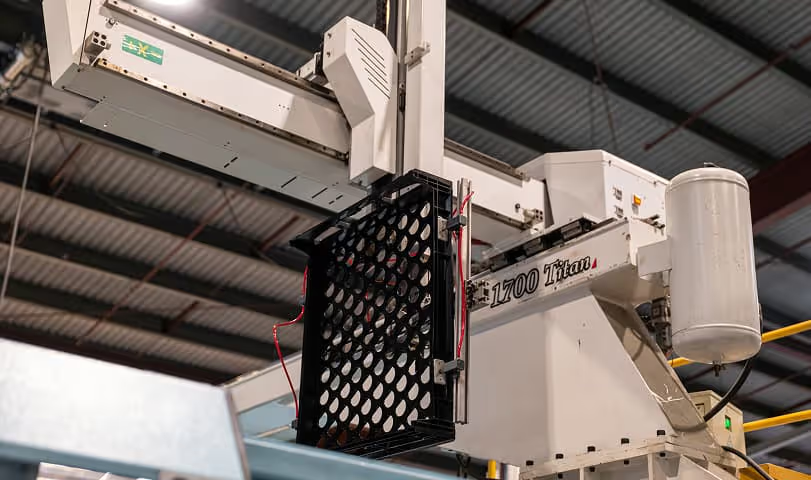
Machine range and capacities
Our facility features injection moulding machines ranging from 50 to 450 tonnes.
This allows us to produce components of all sizes - from small precision parts to large industrial products - with consistent quality and efficiency.
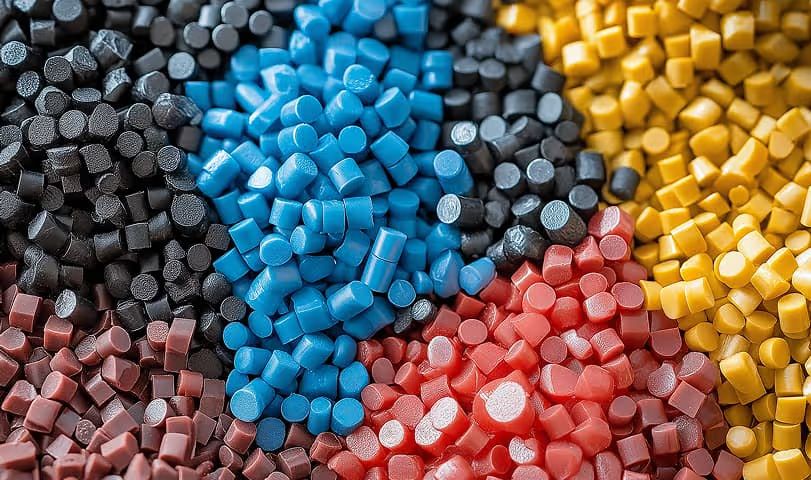
Materials expertise
We work with diverse plastics tailored to your requirements: standard polymers for everyday applications, engineering-grade materials for demanding environments, specialty options with UV and flame resistance, plus sustainable alternatives including recycled and bio-based polymers.
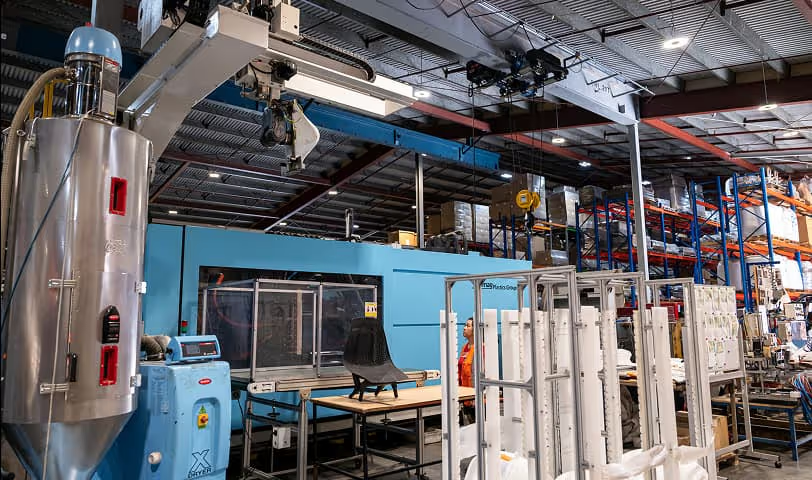
Production capabilities
Our manufacturing spans prototype development for concept testing, small batch production for market trials, high-volume manufacturing for commercial scale, and just-in-time production to support your inventory requirements.
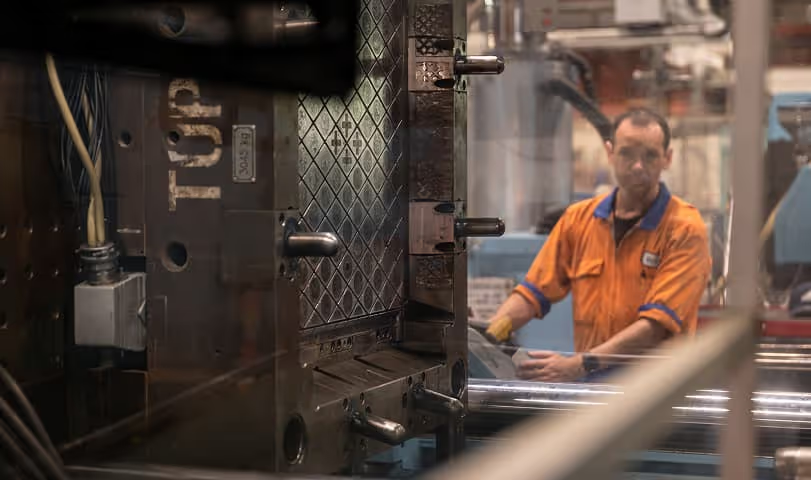
Advanced features
Our technical capabilities include multi-cavity tooling, insert moulding, overmoulding, precise colour matching, and advanced cooling systems. These technologies ensure efficient production while maintaining exceptional quality.
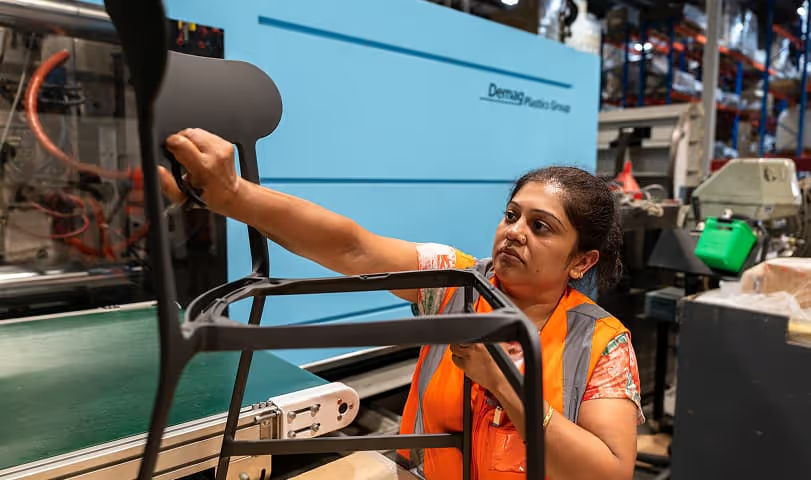
Quality assurance
Our ISO 9001 certified quality system includes dimensional verification, visual inspection, material testing, and comprehensive documentation. Every component undergoes thorough quality checks before delivery.
FAQs
Explore our frequently asked questions to understand injection moulding better and make informed decisions.
Injection moulding is a manufacturing process used to produce parts by injecting molten material into a mould. This technique is widely used for creating complex shapes with high precision. It is ideal for mass production of plastic components.
Common materials for injection moulding include thermoplastics, thermosetting polymers, and elastomers. Each material offers unique properties suitable for different applications. The choice of material impacts the performance and durability of the final product.
The time required for injection moulding depends on the complexity of the part and the production volume. Typically, the process can take anywhere from a few seconds to several minutes per cycle. Efficient design and tooling can significantly reduce production time.
Injection moulding is often cost-effective for large production runs due to its efficiency and speed. The initial investment in mould creation can be high, but costs decrease significantly with higher volumes. It offers a competitive edge for manufacturers looking to scale.
Benefits of injection moulding include high production rates, consistent quality, and the ability to create complex geometries. It also allows for minimal waste, making it a sustainable choice. Additionally, it supports a wide range of materials and finishes.
Why choose Uniplas?
Made in
New Zealand
Local manufacturing ensuring quality control, Shorter lead times, and manufacturing transparency.
Sustainable manufacturing
Committed to environmental responsibility with one of NZ's largest rooftop solar installations and sustainable practices.
ISO 9001
certified
Internationally recognised quality management system ensuring consistent, high-quality output.
Engineering
expertise
Decades of injection moulding experience combined with advanced manufacturing capabilities.
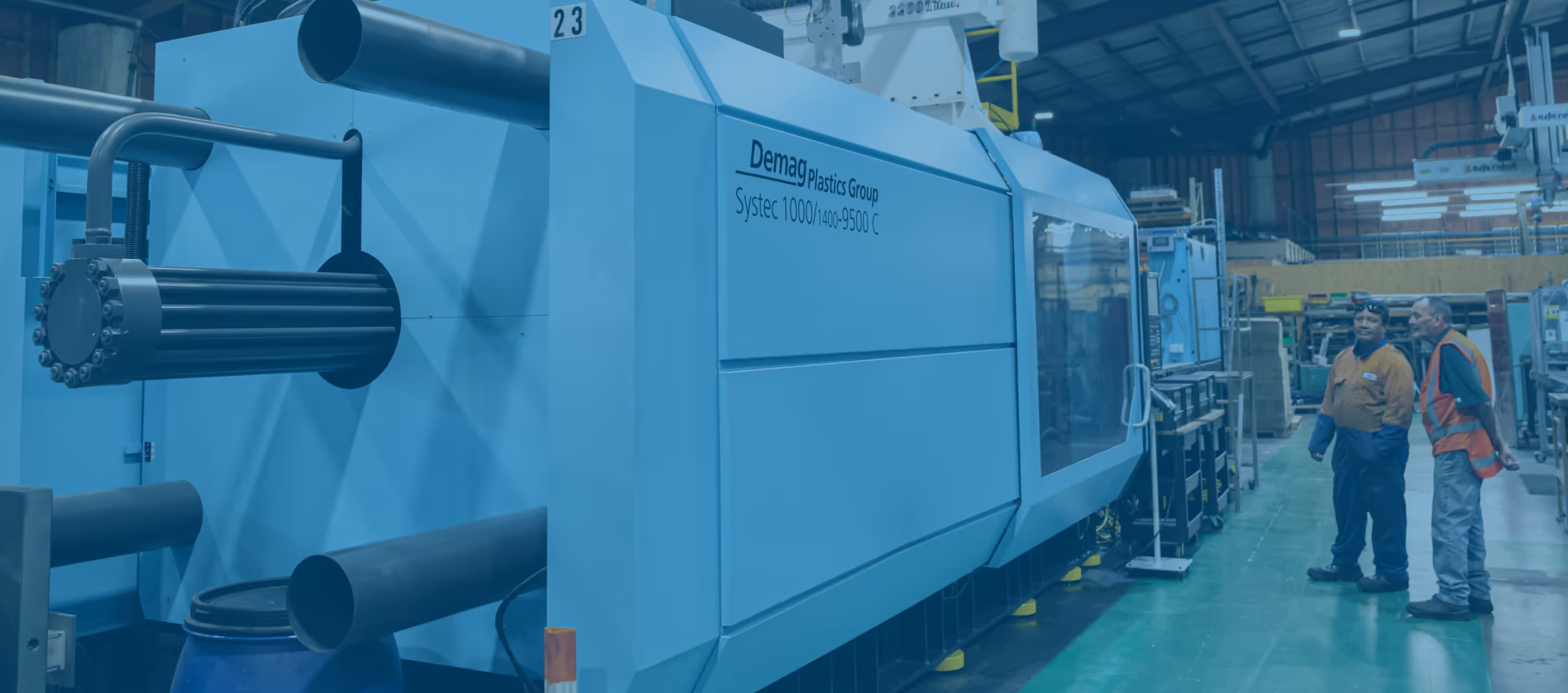
Send us a message
We typically respond within 24 hours.
Our Business hours are : Mon-Fri, 9am-5pm
Taita, Lower Hutt
New Zealand